The can is the most commonly used beverage packaging material in life.The aluminum belt of the cans is composed of three kinds of aluminum alloy with three different components: 3004 -can body, 5052- can cover and 5182 -ring pull. Aluminum is the key of the canister.
The 3004 is a variation of 3003 alloy, form-ability, dissolves, good corrosion resistance, used for processing needs to have more good form-ability, high solder-ability good resistance to corrosion products. Because aluminum sheet itself has good oxidation resistance, it is very good to prevent the oxidation and corrosion of the carbonated beverage to the can.
The cans cover is made of
5052 aluminum sheet and the ring -pull is made of
5182 aluminum sheet. The 5052 and 5182 belong to aluminum magnesium alloy, with good corrosion resistance, weld-ability, cold machine-ability, and moderate strength. The surface is very bright after polishing, But magnesium content of 5182 is more than the 5052, and with some silicon, so the weld-ability is better than 5052 alloy, so the 5052 is used for can cover, the
5182 aluminum sheet is used in the ring-pull.
Specification of ring-pull aluminum sheet
1. Alloy No.: 5182, 3004, 5052, 3105, etc
2. Thickness: 0.18-0.5mm
3. Width:20-1800mm
4. Yield strength: 295-395Mpa
5. Tensile strength: 355-430 Mpa
6. Extension rate: 5-7%;
After baked
1. yield strength: 320MPa
2. Tensile strength ≧ 360MPa
3. Elongation rate ≥ 5.5%
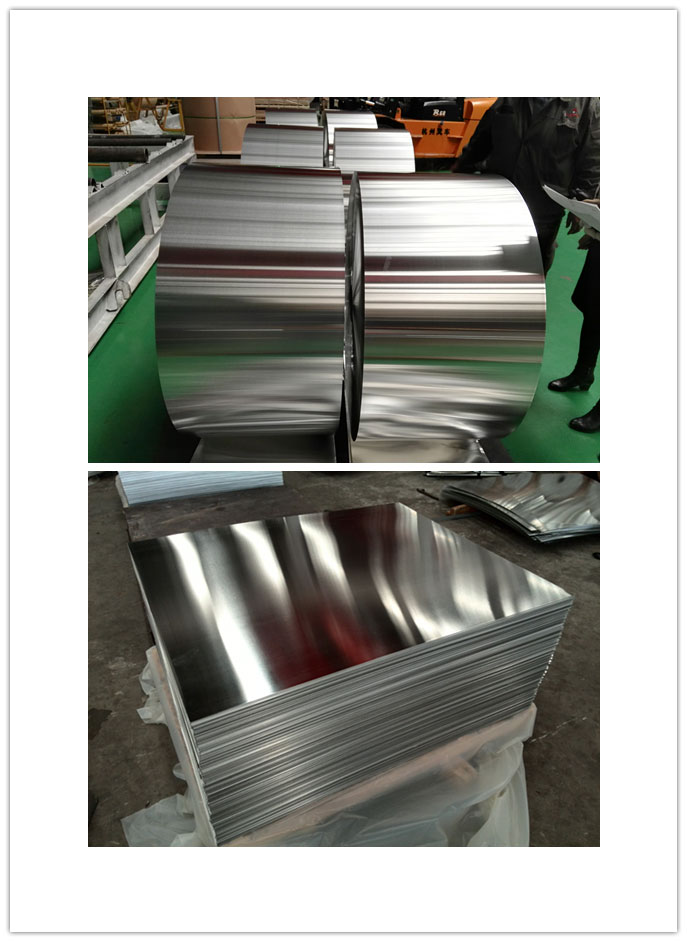
Quality requirement
The production of aluminum cans is more than 40 steps.The main processes related to the performance of aluminum sheet are: blanking, punching cup, thinning drawing, trimming, washing, external printing, internal spraying, drying,Neck, edge, etc. The aluminum sheet must have proper strength and good depth shaping, in order to ensure the continuous blanking process and the yield strength after baking.This includes thickness. The thickness of aluminum sheet is 0.25 ~ 0.30mm, can make it as the round material with a diameter of about 138mm, and then the punch cup is formed by two deep blanks. The reduction rate of the diameter is greater than 50%. after three times of stamping, the thickness is reduced to 0.08 - 0.10mm, the tensile thinning rate is over 65%. Due to the deep processing of the thinning drawing, the extensibility of the blank material is extremely low, so even the small inclusions can make the can broken, then make sure no breakage during trimming and turning.It also requires the material to have good plasticity. After several baking, the shaft of the tank must be kept under pressure and the pressure of the tank bottom is required 1.35kN, the pressure strength of tank bottom is 630kPa, to make sure that the canning and storage can be carried out smoothly.
Because of complexity of the thinning drawing process used in tank forming process, the comprehensive performance of aluminum sheet for tank is very strict. that is, the tensile strength is 270 ~ 310MPa, the yield strength is 250 ~ 300MPa, and the elongation rate is greater than 3%.
The ear rate is less than 2%. There is no visible ripple on the surface of the plate, and the inner and outer surface finish should be uniform, no oxidation, no visible inclusion, compression, spot and other defects.Plate thickness should be uniform,the tolerance must be within 0.005mm.
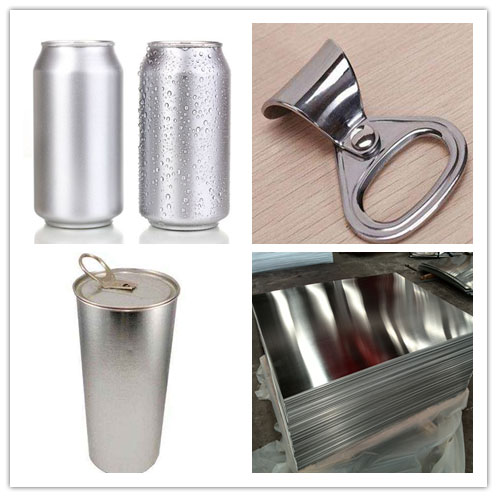
Reduced the earring rate
The control of earring rate is very important. If the ear is formed, it needs to be trimmed, which will waste material and increases the middle cutting process, resulting in increased cost and lower production efficiency. Moreover, the deep impact and thinning drawing process can easily cause cracking between the two ears.The tank material production enterprises to reduce production of ear rate measures taken is mainly control after finishing temperature, the material is in a state of complete re-crystallization, and strict control of cold rolling deformation, eventually make the material of rolling texture of re-crystallization texture about 25%.Of 3104 alloy tank is beneficial to formation during hot rolling temperature higher than 300 ℃ the end of recrystallized cubic texture, increase the proportion of the amount of re-crystallization texture, thus inhibiting the ear rate.The production practice shows that when the l+4 hot continuous rolling line can be used for rolling can, it can be formed by the crystallization cube. More than 85%.After the cold rolling can reach 0.28mmH19 state, the cold rolled texture and the re-crystallization cube can be in the best match state, with the lowest ear rate.
The ear rate is related to the size and quantity of the inclusions in the material, and the impurities and inclusions in the aluminum can have a significant effect on the ear rate.Because the coarse inclusions and impurities have different elastic modulus with the substrate, the flow of the surrounding metal will be impeded in the process of making the cup and the variable book drawing, thus increasing the ear rate.The coarse Al grains also increase the in-homogeneity of metal deformation and make the ear rate high.The smaller the compound particles after homogenization annealing, the more uniform the distribution, the lower the ear rate.
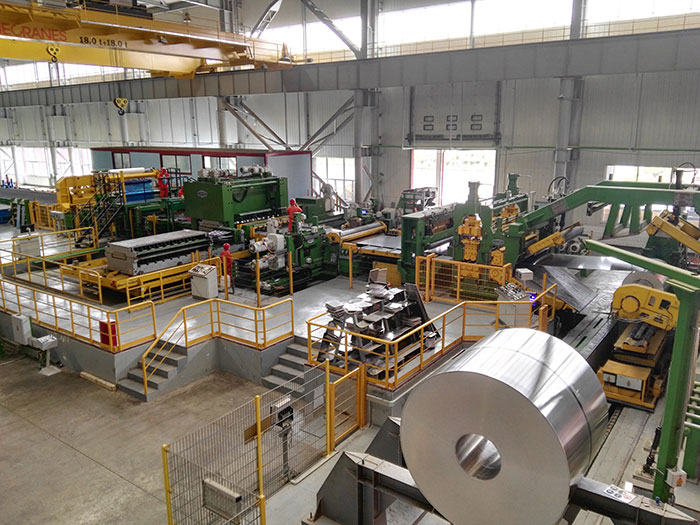